HOME ARTICLE ONLINE PRODUCT SUPPORTThermal Oxidizing System Removes Hydrocarbon Emissions and Reduces Hydrogen Consumption for P/M Industry
Sheridan A. Glen, John R. Martin, Jr. and Hans M. Wenghoefer | Environmental Engineering Corp. | Cranston, RI
Environmental concerns over emissions from thermal processing systems are growing as the industry works to meet more stringent particulate material standards. This article, based on a presentation at the International Conference on Powder Metallurgy and Particulate Materials (PM2TEC), sponsored by MPIF and APMI, May 30 - June 3, 2000 in New York City, describes a thermal oxidizing system that has been developed to significantly reduce the emission of waxy hydrocarbons generated from lubricants used in the powder metallurgy (PM) industry.
During its first three years of operation, Environmental Engineering Corporation (EEC), Cranston, RI, spent considerable time working on a thermal oxidizer for diesel engines. The purpose was to create a commercial product that would perform as a muffler replacement, but be capable of lowering particulate emissions in accordance with the U.S. Urban Bus Retrofit and Rebuild Program, sponsored by the U.S. EPA. The goal of the program is to clean up the exhaust of dirty, pre-1989 city buses. The effort to develop a competitive product for this program created a wealth of information about the dynamics of heat, the thermal properties of various pollutants, and residence time necessary for complete combustion.
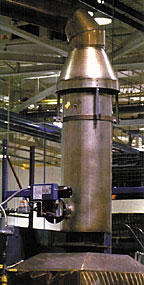 The thermal oxidizer eliminates the emission of waxy hydrocarbons for powdered metal sintering furnaces. |
During one of the frequent tours of the company's facility where a thermal oxidizer prototype had been constructed, a visiting colleague observed that the PM industry could use such a device for combusting waxy emissions. EEC began investigating the powder metallurgy/heat treatment industry and learned that zinc stearate and other blended lubricants are used for binding and die wall friction reduction in powder metal parts production. In heat treating furnaces, especially those designed to sinter powdered metal products at very high temperature, waxy emissions flow up through the furnace hood and result in air pollution and noxious odors being vented to the outside atmosphere. These pollutants also condense on the inside walls of the flue, creating a serious fire hazard.
The lubricant can represent as much as 2% of the total product by weight, resulting in emissions of more than 5 lbs./hr. depending on how much product is loaded into the furnace and the mass of each part. The industry, in fact, does emit a significant amount of waxy hydrocarbons to the outside air, indoor air, and as condensation inside the stack walls.
PROTOTYPE DEVELOPMENT
The first prototype utilized a ring burner that worked well, but the gas outlet holes at the top would have clogged if the operator ran the furnaces without constant use of the thermal oxidizer. Working with several companies under contract, EEC came to the conclusion that the most effective approach would be to introduce heat into the combustion chamber on the tangent. This concept created a swirl zone that allows for better mixing and heat transfer after the gases exit the furnace hood.
A small static furnace was constructed to test binders and lubricants and it was found that these materials begin to decompose at about 400° F and would combust if the residence time was at least 0.4 seconds, making some assumptions about flow characteristics of PM furnaces. Furnace operators typically introduce atmosphere at not greater than 8000 cfh in large continuous belt models. Gas flows through the front hood represent about 2/3 of the total introduced gas mixture. The test protocol used to analyze the behavior of the lubricants and the attendant results were monitored by staff engineers at a well-known furnace company and results were reviews by over 10 prospective customers.
Refinements in design were introduced in four subsequent prototypes. The final design (marketed as Thermo-Stack) incorporates a cylindrical thermal oxidizer, made from 304 stainless steel and lined with ceramic fiber that very effectively uses the concept of time and temperature to combust the hydrocarbon emissions. Other maintenance considerations required that the device be robust and easy to install on existing furnaces to minimize downtime and operational costs.
DESIGN AND CAPABILITIES
The unit measures approximately 48" high by 16" in diameter. An adjustable, gas-fired, 50,000 - 300,000 Btu/hr integrated burner heats the chamber to over 1500° F. Hydrocarbon emissions carried by the furnace gases enter the chamber through the front furnace hood. The tangentially-fired gas burner fires into the combustion zone where it adds incremental heat to the furnace exhaust stream. Tests have shown that the temperature within the burner chamber is quite uniform (20° F) from side-to-side of the cylindrical chamber as a result of the burner firing tangentially to the interior refractory wall. This causes the exhaust entering from the bottom of the chamber to swirl and mix, resulting in even heat distribution.
A unique slide gate damper is mounted below the burner to adjust the flow of exhaust into the thermal oxidizer. The slide gate damper is adjusted so that there is a slight negative pressure in the hood. This means that all the exhaust from the furnace flows up the stack, without excessive air entrapment that tends to cool the exhaust. It is imperative for best performance of the device that the exhaust gases coming from the hood of the furnace should be as hot as possible, preferably at a minimum 900° - 1000° F.
Air inlets also allow for combustion air to be added to the flow inside the chamber in applications where furnace inflow is very low. There is usually sufficient oxygen content in the exhaust gases to effectuate complete hydrocarbon combustion. If necessary, additional make up air can be introduced below the burner with the adjustable grill.
Temperature readings are taken using a thermocouple with digital readout. Temperature profiles of the chamber taken from the combustion zone at the bottom to the top of the thermal oxidizer show a temperature drop of about 15%. The temperatures within the chamber are affected by several factors, in addition to the output of the burner. They include the temperature of the exhaust stream coming from the furnace and the heat value of the hydrocarbons within that exhaust stream.
Based on gas analysis using an ECOM gas analyzer, opacity meter and odor assessment, temperatures of 1400° - 1600° F are sufficient to eliminate odors and successfully burn hydrocarbons from the exhaust of powdered metal furnaces when residence time within the burner chamber is at least 0.4 seconds (Figs. 2 and 3).
Fig. 2 A gas analysis of the furnace exhaust stream prior to entering thermal oxidizer. (Binder/Lubricant Blend)
Fig. 3 A gas analysis of the corresponding thermal oxidizer exhaust stream. (Binder/Lubricant Blend)
Large quantities of unburned or partially burned lubricant can significantly increase temperatures within the chamber. On the other hand, large amounts of ambient air entering the device with the furnace exhaust stream can significantly lower the temperatures within the burn chamber, requiring an increase in burner output. Long, uninterrupted exhaust stacks can create chimney effects causing significant drafts. This can cause gases to be drawn from the furnaces and can create negative pressures in buildings both causing increased gas and fuel consumption.
In furnaces where hydrogen in the gas mix has traditionally been increased to maintain a very robust flame curtain (the purpose being to effectuate more complete combustion of the hydrocarbon emissions), experience has allowed some furnace operators who have installed the thermal oxidizer to dial down hydrogen use by as much as 15%. The device accomplishes emissions combustion, not an overly robust flame curtain.
A hood installed above the device allows cooling air to be introduced to the exhaust stream assuring that exhaust flow into the galvanized conduit and up to the roof is not over 500° F. An optional cladding can be installed which forces radiant heat from the unit up into the hood, keeping the local air temperature lower. With the burner set at minimum Btu output, the unit uses only 1.8 mm Btu/day (approximately five dollars per day).
SUMMARY
Four thermal oxidizer prototypes were built, each one lighter with more sophisticated liner materials. Peer-reviewed results and the successful implementation of the final design in powdered metal plants have shown that the thermal oxidizer can efficiently reduce hydrocarbon-based lubricant emissions from PM sintering furnaces by over 90%, provided residence time within the burn chamber is greater than 0.4 seconds at 1400° - 1600° F.
The refractory in the burner chamber is designed for long life, with flame abrasion resistance. Installation is relatively simple; the unit can be mounted directly to the furnace hood. A low maintenance AGA and CGA certified burner can be fired with natural gas or propane and has built-in flame safety. The unit weighs approximately 125 lbs., so most hoods will support the unit with lateral stability provided by an angle-iron frame or overhead hangers.
The company is currently evaluating smaller and larger designs for various furnace sizes and is investigating other markets such as carbon sintering, textile manufacturing, and chemical equipment manufacturing for potential applications.
For further information regarding ThermoStack systems, contact Thermo-Stack, LLC at 888.332.7654 or email info@thermo-stack.com.
This article first appeared in the September 2000 issue of Industrial Heating.
HOME ARTICLE ONLINE PRODUCT SUPPORT